How to Commission Your European-Style Wire Rope Electric Hoist
A step-by-step guide to ensure safe and efficient commissioning of your European-style wire rope electric hoist.
Commissioning your European-style wire rope electric hoist is an essential process to ensure its safe and efficient operation. It's more than just installation; it's about confirming that the hoist is set up properly for long-term performance.
Proper commissioning minimizes risks, prevents accidents, and ensures the hoist operates at peak efficiency. This process is crucial to extend the hoist's lifespan and avoid costly repairs or downtime.
Why Proper Commissioning Matters
- Safety: Proper commissioning ensures all safety mechanisms are functioning to avoid accidents.
- Efficiency: A well-commissioned hoist ensures smooth operations and reduces delays.
- Longevity: Correct installation and testing prevent wear and tear, helping to extend the hoist’s service life.
Key Steps for Successful Hoist Commissioning
- Pre-Commissioning Checks: Before starting, verify that all components are in place and meet specifications.
- Electrical Equipment Inspection: Ensure that all electrical wiring complies with wiring diagrams and local safety standards.
- Movement Testing: Verify that the hoist moves smoothly in all directions, checking both hoisting and traveling motions.
- Safety Features Check: Test emergency stop functions, limit switches, and overload protection mechanisms to ensure they work properly.
- Operator Training: Train operators on proper hoist use and safety procedures to avoid misuse and increase safety.
Each of these steps is essential in ensuring your hoist will operate correctly and safely from day one. Let’s explore these steps in more detail to understand how to carry them out effectively.

European style electric wire-rope hoist 3 ton to 80 ton for sale , good price
Pre-Commissioning Preparations
Proper pre-commissioning is crucial to ensure the hoist operates safely and efficiently. This step involves checking compliance with regulations, correctly positioning the hoist, and preparing for future maintenance. Taking the time to thoroughly prepare will help avoid operational issues later on.
Ensure Compliance with Local Regulations
- Safety Standards: Ensure that your European-style wire rope electric hoist complies with all relevant safety standards, including those set by organizations like ISO, FEM, and local regulatory bodies. These standards typically cover aspects such as electrical wiring, load limits, and structural integrity. A compliance checklist should be in place to ensure the hoist is fully compliant.
- Installation Codes: Double-check that the installation meets local installation codes. This includes adhering to regulations related to electrical connections, load-bearing structures, and proper foundation settings for the hoist and crane. Installation mistakes here could lead to operational failures or unsafe working conditions.
- Inspection Requirements: In some cases, the hoist may require a certification or inspection by a third-party inspector. Ensure that this is arranged in advance to avoid delays during the commissioning process. In addition, confirm that regular inspection schedules are in place according to local industry standards.
- Environmental Considerations: If the hoist will operate in extreme environments such as corrosive atmospheres, high-temperature areas, or areas with fluctuating humidity, make sure the hoist is equipped with the necessary protective features. For example, an explosion-proof hoist might be required in hazardous locations. Check that the hoist components are specifically designed for these environments, including corrosion-resistant materials or temperature-resistant electrical systems.
Hoist Setup and Positioning
- Correct Placement on Crane or Installation Platform: Before beginning the installation, ensure that the hoist is properly positioned on the crane or installation platform. The hoist should be placed in such a way that it aligns with the crane’s lifting axis and track system. Improper alignment can lead to uneven load distribution and inefficient operation.
- Adequate Space for Safe Operation: The surrounding space should be sufficient for safe hoist operation. Ensure that there is enough clearance around the hoist for the lifting hook to move freely without hitting any obstacles. Check that the hook can fully extend in all directions without obstruction. Adequate space ensures that the hoist operates smoothly, without risk of accidental damage or injury to personnel.
- Track Installation and Alignment: If the hoist is mounted on a trolley system, make sure the tracks are installed properly and are level. Misaligned tracks can cause the trolley to jerk or even derail, leading to potential system failure or dangerous situations. Verify that the track gauge is consistent and that the track is supported properly across its entire length.
- Access for Maintenance and Servicing: When positioning the hoist, ensure that there is easy access for future maintenance, servicing, and inspections. Avoid placing the hoist in tight, hard-to-reach spaces, as this will complicate repairs and regular checks. Consider the ease of access to electrical panels, controls, and hoisting components. Proper access helps maintain the hoist’s longevity and ensures that safety inspections can be conducted regularly without hindrances.
Taking these pre-commissioning steps seriously ensures that your hoist setup will be both efficient and safe, minimizing operational disruptions and ensuring a smooth commissioning process. Once these preparations are completed, you can move forward to conducting inspections and functional tests to ensure the hoist works as expected.
Initial Inspections Without Load
Before putting any load on the hoist, it’s essential to conduct thorough inspections to ensure everything is in proper working order. These checks help identify any potential issues early, allowing for adjustments before the hoist is used under load.
Electrical Equipment Check
- Verify Electrical Connections: Start by checking all electrical connections. Ensure that they are securely connected according to the hoist’s wiring diagrams and that the connections meet local electrical regulations. Loose or faulty electrical connections can cause operational failures or safety risks. Pay special attention to any connections that impact the hoist's control system and safety features.
- Inspect Cable Routes: Examine the hoist’s cable routes to make sure that the cables are not exposed to wear and tear. The cables should be properly secured and routed in a way that prevents them from snagging or getting caught on surrounding structures when the hoist moves. This will help avoid electrical faults or physical damage to the hoist.
Push Button Controller Check
- Ensure Condition of Controller and Cables: Inspect the condition of the push button controller and the pendant cables. Look for any signs of wear, fraying, or damage that could compromise the controller’s functionality. The controller should be positioned at an appropriate height, easily accessible to the operator, and within reach for safe operation.
- Test Functionality of All Direction Buttons: Press each direction button on the controller and verify that the corresponding movement happens in the correct direction. Ensure that both the hoist’s up and down functions, as well as the trolley’s forward and backward movements, are working as intended. If any direction is reversed or non-responsive, check the power supply's phase sequence and make adjustments as necessary.
- Check Emergency Stop Button Operation: Test the emergency stop button to ensure it functions correctly. The emergency stop should immediately halt all hoist movements when pressed. Verify that the button is easy to access and that it doesn’t require excessive force to activate. This is crucial for ensuring that operators can stop the hoist quickly in case of an emergency.
Sound and Vibration Inspection
- Assess Sound Levels During Operation: Run the hoist through its basic functions (hoisting and traveling) while observing the sound it produces. Listen carefully for any abnormal noises, such as grinding, squealing, or clanking. Unusual sounds can indicate installation errors, such as misalignment, or could be signs of worn-out components that require attention.
- Check for Unusual Vibrations or Noises: Feel the hoist’s frame and components for any unusual vibrations while the hoist is in motion. Strong or intermittent vibrations during travel or hoisting could indicate issues with the power supply or an improperly installed trolley on the track. If vibrations or noises persist, investigate further to identify the cause, and do not use the hoist until the issue is resolved.
Completing these inspections without a load ensures that your hoist is in optimal condition before it starts operating under normal working conditions. Identifying and resolving any issues at this stage helps prevent downtime and ensures safe, efficient operation once the hoist is under load.
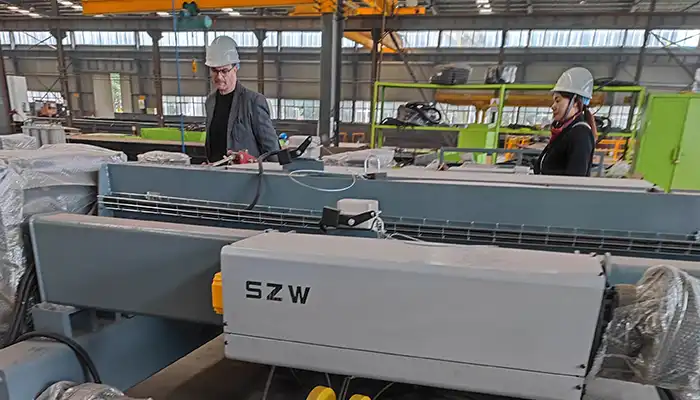
4 main types of electric wire rope hoists for your selection
Testing Hoist Movement and Load Handling
Once the initial inspections are completed and all electrical components are in good condition, it’s time to test the hoist's movement and load handling capabilities. These tests will confirm that the hoist operates smoothly and safely under various conditions.
Initial Motion Testing
Check Upward, Downward, and Horizontal Movements Without Load: Begin by testing the hoist’s movement in all directions—upward, downward, and horizontal (if applicable) without any load. This helps to ensure that all basic movements are working correctly.
- Observe the hoist as it moves in all directions. The movement should be smooth, with no jerking or hesitation.
- Listen carefully for any abnormal sounds, such as grinding or scraping. Any unusual noise could indicate misalignment, improper lubrication, or other mechanical issues.
- Pay attention to the responsiveness of the hoist controls. Ensure the hoist starts, stops, and changes direction promptly and smoothly.
Verify Smooth Operation and Absence of Abnormal Noise: Smooth operation is essential for safe and efficient hoist performance. If you hear grinding, scraping, or clanking noises during movement, it may signal a need for further inspection and adjustment. These noises can often indicate loose parts, alignment issues, or insufficient lubrication. If all movements are smooth and the hoist operates quietly, this indicates that the installation was done correctly.
Verify Load Control
Test Hoist with a Small Load: After the hoist has passed the motion testing without load, it’s time to test it under a small load. Use a manageable weight to verify the hoist’s lifting and lowering functions.
- Slowly raise and lower the load while monitoring the hoist’s performance. Check that the load moves smoothly and evenly without any jerks or pauses.
- Pay attention to the hoist's lifting speed and control. It should lift and lower the load at a steady, consistent pace.
Ensure Load Stability and Smooth Operation at Different Lifting Heights: Test the hoist at various lifting heights to ensure stability and consistent operation across the entire lifting range.
- As you raise and lower the load, check that the load remains stable and doesn’t sway or tilt unexpectedly.
- Ensure that the hoist operates smoothly at different heights. If the hoist struggles or becomes erratic at higher or lower lifting points, it may indicate issues with the hoist’s motor, lift mechanism, or track alignment.
These tests help confirm that the hoist is capable of handling loads effectively and operates smoothly at various lifting heights. If any issues are detected during these tests, they should be addressed before moving forward with full-scale operations.
Safety Checks and Adjustments
Ensuring the safety of your hoist during operation is crucial to prevent accidents, equipment damage, and personnel injury. This section covers essential safety checks and adjustments to confirm that all protective systems are functioning as intended.
Check Overload Protection
Test Overload Limiters
- Goal: Ensure that the hoist’s overload protection systems are operational.
- How to Test: Gradually apply a load that exceeds the hoist's rated capacity. The overload protection should automatically stop further movement to prevent damage.
- What to Look For: The system should trigger at the correct overload threshold without allowing the hoist to operate beyond safe limits.
Confirm Overload Protection Functionality
- Action: Double-check that the overload protection mechanism properly halts operation when the rated load is exceeded.
- Why It's Important: This prevents damage to the hoist and protects operators from working under unsafe conditions.
Check Emergency Stops and Limit Switches
Test Emergency Stop Function
- Goal: Ensure the emergency stop button halts the hoist's operation immediately when pressed.
- How to Test: Press the emergency stop and verify that the hoist comes to a complete halt in all movement modes.
- What to Look For: The hoist should stop quickly and safely, with no delayed response.
Inspect Limit Switches
- Goal: Ensure limit switches function as intended to stop the hoist at maximum height or travel limit.
- How to Test: Manually run the hoist to its travel limits and verify that the limit switches prevent further movement.
- What to Look For: Ensure smooth operation of the limit switches without failure or hesitation.
Verify Braking Systems
Check Brake Engagement
- Goal: Confirm that the hoist's braking system works effectively during load holding.
- How to Test: Lift a load and let it rest while the brakes engage. The load should remain stationary without any noticeable slippage.
- What to Look For: Ensure the brakes hold the load securely, and check for any signs of delayed engagement or failure.
Safety checks are crucial to verify the proper functioning of all safety systems in your hoist, including overload protection, emergency stops, limit switches, and braking systems. Thorough testing and adjustments are essential to ensure the hoist operates safely and meets all safety standards. Address any malfunctions immediately to maintain the safety and longevity of the equipment.
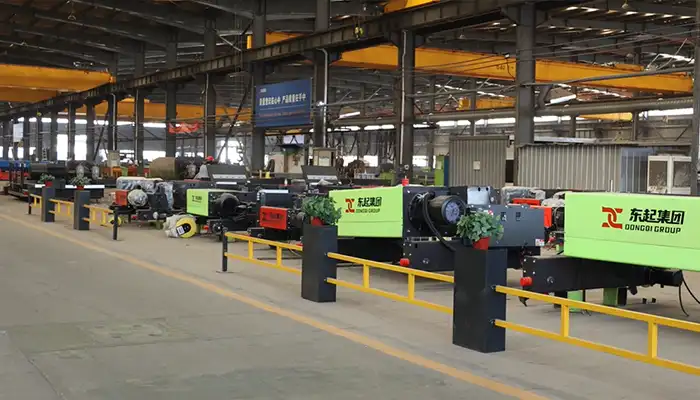
Customized for your needs, check the electric wire rope hoist specifications
Post-Commissioning Review
After the hoist has been successfully commissioned and tested, it is essential to conduct a final review. This ensures that everything is set up correctly and that the hoist will function safely and efficiently in its operational environment.
Verify Correct Operation and Calibration
Double-check Operational Settings
- Goal: Confirm that all operational settings are properly calibrated.
- How to Verify: Reassess the settings such as lifting height, speed adjustments, and limit switch positions to ensure they are correctly configured for safe and efficient operation.
- What to Look For: Verify that all settings match the manufacturer’s specifications and the specific requirements of your operation.
Reassess Safety Features
- Goal: Review all safety systems to ensure they are fully operational.
- How to Verify: Recheck the overload protection, emergency stops, and braking systems.
- What to Look For: Confirm that all safety features engage correctly and provide the necessary protection during operation.
Overall Functionality
- Goal: Ensure the hoist operates smoothly without any issues.
- How to Verify: Perform a final test cycle to ensure the hoist works properly under both no-load and load conditions.
- What to Look For: Watch for any unusual noises, vibrations, or delays during operation that could indicate an issue.
Record Documentation
Complete Installation and Inspection Reports
- Goal: Create a detailed record of the installation and all inspections conducted.
- What to Include: Document the hoist's serial number, installation date, tested settings, and results of all inspections and tests.
- Why It’s Important: These records are valuable for future reference, warranty claims, and compliance with safety regulations.
Maintain Test and Adjustment Records
- Goal: Keep a record of all tests, adjustments, and safety checks performed.
- How to Maintain: Log each test's outcome, adjustments made, and any issues that were addressed.
- What to Look For: Ensure that each step of the commissioning process is thoroughly documented and stored for future reference.
The post-commissioning review is the final step to confirm that your hoist is fully operational and safe. Double-checking all settings, recalibrating as needed, and ensuring that all safety features work correctly are essential steps. Don’t forget to document everything for future reference and compliance. This ensures a smooth start-up and long-term, trouble-free operation.
Operator Training and Handover
Once the hoist is commissioned, it’s crucial to ensure that operators are fully equipped to use it safely and efficiently. Proper training and a thorough handover process will help maintain the hoist’s longevity and performance.
Provide Operator Training
Goal: Ensure operators are well-trained on hoist operation, safety, and maintenance.
What to Include in Training:
- Hoist Operation: Teach operators how to use the hoist, including basic movements (lifting, lowering, and horizontal motion), load handling, and emergency operations.
- Safety Procedures: Cover safety protocols such as emergency stop procedures, overload protection, proper load handling, and personal protective equipment (PPE) requirements.
- Routine Maintenance: Instruct operators on daily or weekly maintenance tasks, like inspecting cables, checking for wear and tear, and performing lubrication tasks.
- Troubleshooting: Provide guidance on identifying and resolving common operational issues, including what to do if the hoist stops working or produces unusual sounds.
Why It’s Important: Properly trained operators reduce the risk of accidents, increase the lifespan of the hoist, and help maintain a smooth and efficient workflow.
Handover to the Client
Goal: Complete the final handover process and ensure the hoist is ready for use.
Key Steps:
- Review Final Checklists: Go through the checklist of inspections and tests completed during the commissioning process. This ensures that no steps were missed and that everything is in place.
- Explain Hoist Features: Walk the client through the hoist’s key features and controls, highlighting safety mechanisms, maintenance routines, and operational settings.
- Provide Documentation: Hand over all relevant documents, including the installation report, maintenance schedule, and warranty information.
Why It’s Important: A successful handover ensures the client has a complete understanding of the hoist’s operation and safety features. This also serves as a final check to make sure the hoist meets all requirements before use.
Operator training and a thorough handover are essential steps for ensuring safe and efficient operation of the hoist. Providing clear, comprehensive training helps prevent accidents, reduces wear and tear, and ensures that operators are prepared to maintain the hoist in top condition. The handover process confirms that everything is ready for use and that the client is confident in the hoist's capabilities.
Conclusion
The successful commissioning of your European-style wire rope electric hoist involves several critical steps to ensure safe and efficient operation. From pre-commissioning preparations and inspections to operator training and the final handover, each phase plays a vital role in guaranteeing the hoist operates at its best.
Recap of Commissioning Steps
- Pre-Commissioning: Verify compliance with regulations and ensure proper hoist setup.
- Initial Inspections: Inspect electrical systems, controls, and safety features.
- Testing Hoist Movement: Check hoist operation with and without load to ensure smooth functionality.
- Safety Checks: Confirm overload protection, emergency stops, and brakes are working properly.
- Post-Commissioning Review: Reassess operation and document findings.
- Operator Training and Handover: Equip operators with the knowledge to safely use and maintain the hoist.
Emphasis on Safety, Efficiency, and Long-Term Performance
The primary goal of commissioning is to ensure the hoist is ready for safe, efficient, and reliable operation. A well-commissioned hoist can perform consistently over its lifetime while minimizing risks to both personnel and equipment. Prioritizing safety features like overload protection and emergency stops not only protects the operator but also prolongs the hoist’s lifespan.
Reminder to Perform Regular Maintenance and Safety Checks
Once commissioned, it’s important to establish a routine of regular inspections and maintenance. Ongoing checks for wear and tear, proper lubrication, and safety system functionality help keep the hoist in optimal condition. Regular maintenance ensures that the hoist continues to operate smoothly, reducing downtime and preventing costly repairs.
In summary, commissioning is a crucial process that sets the foundation for safe and effective hoist operation. By following the steps outlined and maintaining a strong focus on safety and performance, you can ensure that your hoist remains a reliable asset for years to come.
Article by Bella ,who has been in the hoist and crane field since 2016. Bella provides overhead crane & gantry crane consultation services for clients who need a customized overhead travelling crane solution.Contact her to get free consultation.